Industrial flanged pumps: solution for high pressure applications
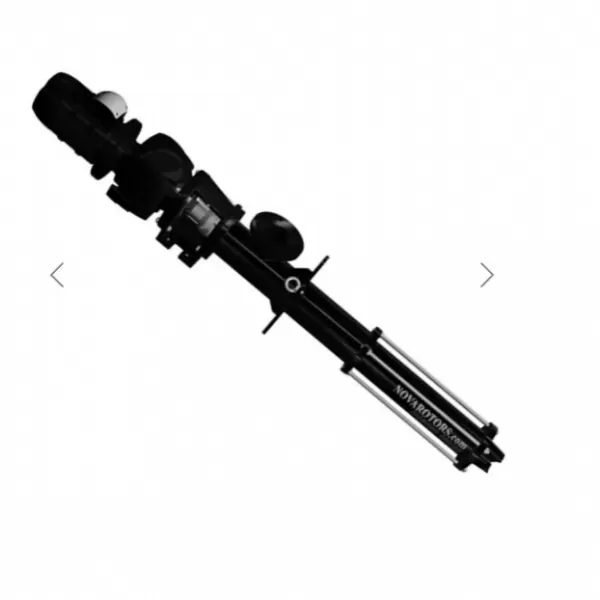
Introduction to critical connection technologies
In the contemporary industrial landscape, flanged industrial pumps represent the most reliable technological solution for applications requiring high performance, operational safety and ease of maintenance. Nova Rotors has developed a complete range of industrial sector pumps with advanced flanging systems, designed to meet the most critical needs of the oil, offshore and industrial market.
Pipeline pumps and offshore platform pumps require exceptional construction standards, where each component must guarantee absolute reliability in extreme operating conditions. Nova Rotors flanging technology combines engineering innovation, advanced materials and compliance with the most rigorous international standards.
Fundamentals of flanged technology
Historical evolution and structural advantages
Flanging technology in flanged industrial pumps has evolved significantly in recent decades, moving from standard solutions to highly specialized systems. Nova Rotors has contributed to this evolution by developing connection systems that guarantee:
Perfect sealing: Total elimination of leaks through precision geometries and advanced sealing materials.
Structural resistance: Ability to withstand operating pressures up to 300 bar with safety margins superior to industrial standards.
Ease of maintenance: Quick access to internal components without the need to disconnect main pipelines.
Application versatility: Compatibility with different plant configurations and multiple orientation possibilities.
Advanced design principles
The design of Nova Rotors flanges follows rigorous engineering criteria:
Finite element analysis (FEA): Each flange is optimized through computational simulations that analyze stress distribution under maximum operational loads.
Anti-fatigue design: Implementation of geometries that minimize stress concentrators and maximize cyclic fatigue resistance.
Weight optimization: Reduction of overall weight without compromising structural performance, crucial for offshore applications.
Types of flanges and available configurations
Flanges according to international standards
Nova Rotors produces industrial sector pumps with flanges compliant with major world standards:
ANSI/ASME B16.5: American standard for carbon steel and stainless steel flanges, with pressure classes from 150# to 2500#. Particularly used in North American petrochemical industry and for intercontinental pipeline pumps.
DIN/EN 1092: European standard covering flanges in steel, cast iron and special materials. The PN (Pressure Nominal) series varies from PN6 to PN400, ideal for European industrial applications and process plants.
JIS B2220: Japanese standard widely used in Asia and for international projects requiring compatibility with Japanese technologies.
API 676: Specific standard for the petroleum industry, used in offshore platform pumps and hydrocarbon production plants with extreme pressures.
API 682: is an international standard, adopted in our pumps specifically developed for the design and supply of mechanical seals, cartridge seals and related auxiliary systems, particularly widespread in the Oil & Gas industry.
Specialized geometric configurations
Raised Face (RF) flanges: Raised sealing surface that ensures concentration of tightening pressure on the gasket, ideal for medium pressures and non-aggressive fluids.
Flat Face (FF) flanges: Flat sealing surface used for applications with large surface gaskets, typical of low-pressure systems with viscous fluids.
Ring Type Joint (RTJ) flanges: Metal ring configuration for high pressure and temperature applications, standard in offshore platform pumps and cryogenic plants.
Tongue and Groove (T&G) flanges: Male-female system that ensures self-centering and superior sealing, used for dangerous or highly volatile fluids.
Advanced materials for critical applications
Duplex and superduplex stainless steels: Used for pipeline pumps that transport corrosive fluids or operate in aggressive marine environments. The biphasic structure guarantees superior corrosion resistance and excellent mechanical characteristics.
High-strength alloys: Inconel, Hastelloy and other superalloys for high temperature and pressure applications, typical of petrochemical and geothermal industries.
Protective coatings: Application of ceramic and polymeric coatings to increase wear and corrosion resistance in specific applications.
International compliance standards and certifications
Safety and quality standards
Nova Rotors flanged industrial pumps comply with the most rigorous international standards:
For pressure equipment Pressure Equipment Directive (PED) 2014/68/EU: Compliance with the European directive for pressure equipment, guaranteeing operational safety in the European Union.
ASME Boiler and Pressure Vessel Code (BPVC): Certification according to the American code for pressure equipment, globally recognized as a safety reference.
API Standards: Compliance with American Petroleum Institute standards for the petroleum industry, including API 676 and API 685.
ISO 9001:2015: Certified quality management system to ensure consistency in performance and product reliability.
Quality controls and conformity tests
Hydrostatic tests: Each pump is subjected to pressure tests at 150% of the required pressure to verify the structural integrity of the flanges as well.
Sealing tests (NDE): Specific checks of seals and welds with test fluids to ensure absence of operational leaks.
Dimensional controls: Accurate inspection of all mating surfaces to ensure compatibility with international standards.
Material certification according to EN10204 3.1 or 2.2: Complete traceability of materials used with certificates of origin and chemical analysis of materials employed.
Welding procedures qualified according to UNI and ASME IX WPQR: welding approval certificate in accordance with UNI EN ISO 9606-1:2017 and ASME IX (WPQ)
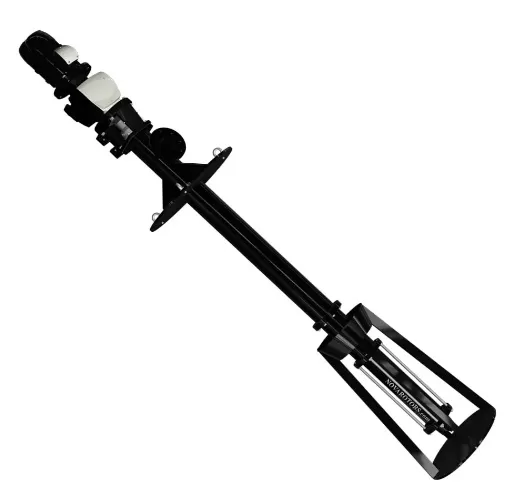
Applications in the oil and offshore industries
Pipeline and gas pipeline pumps
Pipeline pumps represent the most critical application for advanced flanging technologies. Nova Rotors has developed specific solutions for:
Main pumping stations: High-power pumps for long-distance transport with operating pressures up to 300 bar and flow rates exceeding 10,000 m³/h.
Intermediate booster stations: Compact high-efficiency systems for pressure maintenance along the pipeline route.
Loading/unloading terminals: Pumps for rapid transfer between pipelines, tanker ships and storage tanks.
Offshore platforms and marine installations
Offshore platform pumps operate in the most severe conditions of the petroleum industry:
- Production pumps: Management of multiphase fluids with presence of water, oil, gas and sediments in corrosive marine environments.
- Water injection systems: High-pressure pumps for reservoir pressure maintenance and enhanced recovery.
- Fire protection and deluge systems: Emergency pumps for platform safety with absolute reliability requirements.
Refineries and petrochemical plants
In the refining industrial sector, flanged pumps handle:
- Crude oil and intermediate products: Transport of crude oil and distillation fractions with temperatures up to 400°C.
- Finished products: Handling of gasoline, diesel, jet fuels and lubricants with rigorous quality specifications.
- Process utilities: Cooling water, condensed steam and service fluids for support to main processes.
Operational advantages of flanged pumps
Superiority in sealing and reliability
Nova Rotors flanging technology offers decisive advantages over traditional connections:
- Long-lasting sealing: Sealing surfaces machined with micrometric tolerances guarantee perfect sealing even after thousands of pressure cycles.
- Fatigue resistance: Flanges are designed to withstand continuous cyclic loads without degradation of sealing performance.
- Compatibility with advanced gaskets: Possibility to use metallic, spiral metallic and composite material gaskets for specific applications.
Ease of maintenance and accessibility
- Rapid disassembly: Flanged configurations allow access to internal components without disconnecting main pipelines, drastically reducing plant downtime.
- Inspection ports: Possibility to inspect the pump to optimize access during maintenance operations.
- Spare parts standardization: Use of standard components facilitates spare parts warehouse management and reduces maintenance costs.
Installation flexibility
- Plant adaptability: Standard flanges allow integration into existing plants without significant structural modifications.
- Multiple orientation: Possibility of installation in horizontal, vertical and inclined configurations to optimize available space and rotate pump body for side inlets.
- Future expandability: Ease of replacement or upgrade without redesigning the entire piping system.
Advanced design and customization
Specialized application engineering
Nova Rotors offers advanced engineering services for customizing flanged industrial pumps:
- Operating conditions analysis: Detailed study of pressures, temperatures, fluid characteristics and operating cycles.
- Advanced CFD simulations: Fluid dynamic optimization to maximize efficiency and minimize cavitation phenomena.
- Seismic design: Flange dimensioning to resist seismic stresses according to international standards.
Special configurations for critical applications
- Bypass against overpressure: Fluid recirculation systems with overpressure valves
- Temperature and pressure control probes: Solutions for pumped fluids up to 130°C with materials and geometries optimized for thermal expansion.
- Flanges for abrasive fluids: Reinforced configurations with wear-resistant coatings for mining and chemical applications.
Innovative technologies and future developments
Digitalization and intelligent monitoring
The evolution towards Industry 4.0 introduces new possibilities for industrial sector pumps:
Integrated monitoring sensors: Implementation of sensors for continuous monitoring of pump temperature conditions.
Predictive systems: Machine learning algorithms for predicting remaining life of gaskets, stator rubbers and optimal maintenance scheduling.
IoT connectivity: Real-time data transmission for remote monitoring of operating conditions.
Advanced materials and sustainability
High-performance alloys: Development of new materials with superior strength and reduced weight for offshore applications.
Nanotechnological coatings: Application of advanced coatings to increase corrosion resistance and abrasion resistance.
Circular economy: Design oriented to material recovery and reuse to reduce environmental impact.
Automation and robotics
Automatic tightening systems: Development of robotic systems for flange tightening with controlled and repeatable torque.
Automated inspection: Use of artificial vision systems for quality control of sealing surfaces.
Robotic maintenance: Implementation of robotic systems for pump maintenance in dangerous or difficult-to-access environments.
Economic analysis and cost optimization
Optimized Total Cost of Ownership (TCO)
Investment in pipeline pumps with advanced flanged technology generates significant economic benefits:
Reduced maintenance costs: The ease of access and durability of flanges reduce ordinary and extraordinary maintenance costs.
Minimized plant downtime: The speed of maintenance operations reduces downtime and lost production costs.
Energy efficiency: The fluid dynamic optimization of flanged connections contributes to reducing energy consumption.
Comparison with alternative technologies
Advantages over welded connections: Greater flexibility, ease of maintenance and possibility of reconfiguration without permanent modifications.
Superiority over threaded connections: Superior sealing, resistance to high pressures and ease of disassembly.
Comparison with quick couplings: Greater long-term reliability and resistance to cyclic stresses.
Optimal selection and sizing
Selection criteria for specific applications
The choice of offshore platform pumps requires analysis of critical parameters:
Operating conditions: Pressure, temperature, fluid characteristics and installation environment.
Safety requirements: Area classification, applicable regulations and required certification standards.
Installation constraints: Available space, preferred orientation and compatibility with existing systems.
Life cycle: Expected operational duration, maintenance frequency and spare parts availability.
Technical support services
Nova Rotors offers complete support for solution optimization:
Engineering consultancy: Detailed analysis of needs and design of customized solutions.
Operational simulations: Virtual tests to validate performance before installation.
Specialized training: Training of operational and maintenance personnel to maximize efficiency.
After-sales support: Continuous technical assistance and availability of original spare parts.
Flanged industrial pumps: technological excellence for critical applications
Nova Rotors flanged industrial pumps represent the most advanced technological evolution for high-pressure and operationally critical applications. The combination of innovative design, certified materials and compliance with international standards guarantees superior performance in all application sectors.
Investment in advanced flanging technologies generates value through:
- Maximum operational reliability with perfect sealing even in extreme conditions
- Ease of maintenance that reduces operational costs and downtime
- Installation flexibility to adapt to any plant configuration
- Guaranteed regulatory compliance at international level
- Optimized energy efficiency for environmental sustainability
Nova Rotors pipeline pumps and offshore platform pumps continue to establish new performance standards in the industrial sector, anticipating future needs through continuous innovation and attention to sustainability.
For specialized consultancy on selection, sizing and implementation of flanged industrial pumps, the Nova Rotors technical team offers complete support from design to commissioning, guaranteeing optimal solutions for each specific industrial application.
Excellence in critical applications requires superior technologies: choose Nova Rotors technological leadership. Contact us for information!